What is the Cost of Goods Sold?
The cost of goods sold (COGS) includes all the direct costs incurred in manufacturing goods.
The cost of goods sold is a crucial element of a corporation’s income statement, depicting the revenues and expenditures incurred during a specified period. The cost of goods sold is recorded as a part of business expenses.
[ez-toc]
The cost of goods sold represents the cost of doing business.
Ascertaining the cost of goods sold constitutes a significant facet of financial reporting for companies as it aids in determining a company’s gross profit margin and overall profitability.
There is an inverse relation between the cost of goods sold and net income (the bottom line). With an increase in the cost of goods sold, the net income decreases, and with a decline in the cost of goods sold, the net income increases.
COGS for Business Strategy
Organizations must comprehend the constituents of COGS to ensure precise calculation of expenses and make well-informed business decisions like determining the sale price, calculating the break-even point, cushion margin, etc.
Through the analysis of the diverse expenses linked with the cost of goods sold of the merchandise, businesses can discern areas in which cost reductions can be achieved, supply chain optimization can be affected, and profit margins can be enhanced.
Accurate cost of goods calculation plays a vital role in deciding the optimal pricing method for a business. With the true cost of producing or procuring goods, companies can set prices that cover expenses and generate profit while remaining competitive.
Regularly reviewing and updating COGS ensures that businesses can respond to changes in production costs, market conditions, and customer preferences, contributing to long-term financial success.
Components of COGS

The cost of goods sold includes various direct expenses incurred during the production or procurement of goods a company sells. These costs can be grouped into three primary categories: direct materials, direct labor, and manufacturing overheads.
Direct Materials
Direct materials constitute raw materials and component expenses directly related to producing a finished product. They include items such as metals, plastics, and other materials that are transformed during the manufacturing process.
Direct materials costs are calculated by adding the beginning inventory of raw materials to the purchases made during a reporting period and subtracting the ending inventory.
Direct Labor
Direct labor costs are the wages and benefits paid to workers/ laborers directly involved in production. It includes assembly-line workers, machine operators, and other laborers who contribute to creating the finished goods.
Direct labor costs can be determined by multiplying the labor hours worked by the average hourly wage.
Manufacturing Overheads
Manufacturing overheads are indirect expenses that cannot be traced directly to a specific product but are necessary for the production process in a factory.
Factory overhead costs include utilities, factory maintenance, depreciation of equipment, and other indirect expenses incurred in the manufacturing process.
Allocating overhead costs to individual products can be complex, as these costs are distributed across multiple output units.
Examples of COGS
Example 1: Furniture Manufacturing Company
- Direct materials: The cost of wood-ply, nails, screws, and similar raw materials used in furniture production.
- Direct labor: Wages and benefits paid to carpenters, painters, etc., involved in creating the furniture.
- Manufacturing overheads: Expenses such as factory rent, utilities, and depreciation of production equipment.
Example 2: Clothing Retail Company
- Direct materials: The cost of procuring the inventory (purchases) from suppliers in an accounting period.
- Direct labor: Cost of transporting the inventory from suppliers to the retailer’s warehouses or stores.
- Manufacturing overheads: There will be no manufacturing costs involved because the retail business is a tertiary sector involved in the sale and purchase of goods.
For a retail company, the cost of goods sold is computed by adding the beginning inventory to the inventory purchases (including shipping costs) and subtracting the ending inventory.
Example 3: Restaurant
- Direct materials: The cost of ingredients, such as meats, vegetables, and spices.
- Direct labor: Wages paid to chefs, cooks, and other kitchen staff involved in food preparation.
- Manufacturing overheads: Expenses such as kitchen equipment maintenance, depreciation, and utilities.
Cost of Goods Sold for Service-Based Companies
The cost of goods sold is typically associated with businesses that sell physical products. However, service-based businesses may also have the cost of goods sold, although the concept is slightly different. For pure service companies, COGS represents the costs incurred in customer service.
The cost of providing a service can vary depending on the nature of the service. Some service-based businesses have minimal costs, such as consulting businesses, where the primary cost is the consultant’s time. Other service-based businesses may have higher costs, such as landscaping businesses, where the primary costs include labor and equipment.
Examples of COGS for Service-based Businesses
- Consulting Services: A consultant’s primary cost is the time spent providing services to clients. The cost of consulting services may include any travel expenses, research materials, or software used.
- Legal Services: A law firm’s primary cost is the time spent providing legal services to clients. Additional costs can include court fees, research materials, or software.
- Cleaning Services: A cleaning business’s primary cost is the wages of the labor required to provide cleaning services and further may include any cleaning supplies or equipment used.
- Landscaping Services: A landscaping business’s primary costs are labor and equipment.
Calculating Cost of Goods Sold
Accurately calculating the cost of goods sold is essential to assess a business’s financial health and make well-informed decisions.
The calculation of COGS varies depending on the inventory accounting method and inventory costing method used by a company. But, general steps can be followed to calculate cost of goods sold, regardless of the method employed.
Cost of Goods Sold Formula
COGS = Beginning inventory + Inventory Purchases – Ending inventory
This formula applies to the periodic and perpetual inventory systems, though it is primarily associated with the periodic system.
For companies using the perpetual system, the cost of goods sold is updated continuously with each sale, while the periodic system calculates COGS at the end of an accounting period.
For example, a company has a beginning inventory of $ 70,000, makes purchases worth $120,000 during the reporting period, and has an ending inventory worth $40,000. To calculate COGS:
COGS = $70,000 + $120,000 – $40,000 = $150,000
So, the company’s cost of goods sold during the reporting period was $150,000.
Incorporating Direct Labor and Manufacturing Overheads
In addition to inventory costs, businesses must consider direct labor and manufacturing overheads when calculating COGS. Incorporate all the costs by implementing the following steps:
- Determine direct labor costs by multiplying the number of labor hours worked by the average hourly wage for production employees.
- Calculate manufacturing overheads (including utilities, factory maintenance, depreciation of equipment, etc.)
- Add direct labor costs and manufacturing overheads to the inventory costs.
Adjustments for Inventory Costing Methods
Businesses need to modify the calculation of the cost of goods sold (COGS) based on the application of particular inventory costing methods such as FIFO, LIFO, or the weighted average cost method.
Accounting Methods and COGS
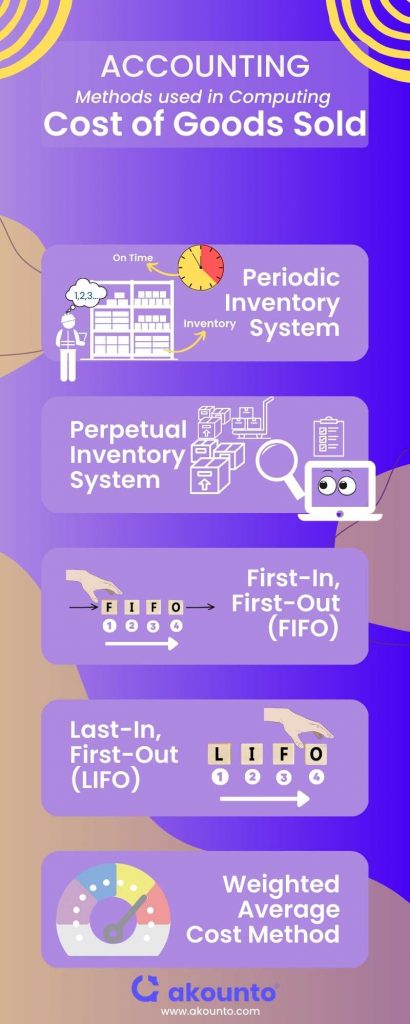
Periodic or Perpetual Inventory Systems
The periodic inventory system only updates inventory records at the end of an accounting period, using physical inventory counts on hand.
In contrast, the perpetual inventory system continuously updates inventory records as purchases and sales occur. The cost of goods sold is calculated and recorded every time a sale is made.
Companies using the perpetual system can have more accurate and up-to-date inventory data, helping them to manage their inventory more effectively.
First-In, First-Out (FIFO)
The FIFO method assumes that the earliest items bought are sold first. Under this method, the cost of goods sold is based on the cost of the oldest items in inventory.
FIFO is useful when inventory items have a limited shelf life or can become obsolete. FIFO tends to produce higher net income when inventory costs are rising, as the lower-cost items are sold first.
Last-In, First-Out (LIFO)
The LIFO method states that the most recently purchased items are the first ones to be sold.
LIFO is often employed when inventory costs are rising, and businesses want to match their most recent costs to current sales revenue, which can result in lower taxes. LIFO may not accurately represent the physical flow of inventory.
Weighted Average Cost Method
The weighted average cost method includes the average cost of all items in inventory and applies this average cost to each item sold. The calculation requires the businesses to divide the total cost of goods for sale by the total units available for sale.
This method smooths out fluctuations in inventory costs and is suitable for businesses with large quantities of similar inventory items.
Cost of Goods Sold and Operating Expenses
Cost of goods sold (COGS) signifies the direct expenses associated with producing or purchasing goods for sale, operating expenses (OPEX) include the indirect costs incurred in running the business.
Understanding the differences between these two expense categories is crucial for accurate financial reporting and decision-making.
Aspect |
Cost of Goods Sold (COGS) |
Operating Expenses |
Definition |
Direct costs related to producing or purchasing goods for sale. |
Indirect costs related to running the business. |
Components |
Direct materials, direct labor, and manufacturing overheads. |
Salaries, rent, utilities, marketing, insurance, and administrative costs. |
Impact on Gross Profit |
Directly affects the calculation of gross profit (Sales Revenue – COGS). |
Does not directly affect the calculation of gross profit but impacts net income. |
Variability |
Typically varies with the level of production or sales. |
Can be fixed or variable, depending on the nature of the expense. |
Accounting Methods |
Affected by inventory accounting and costing methods (FIFO, LIFO, Weighted Average). |
Generally, not affected by inventory accounting methods. |
Example Industries |
Manufacturing, retail, restaurants, and service-based businesses with physical products. |
All businesses, including those with no physical products. |
By differentiating between COGS and operating expenses, companies can accurately report their financial performance and make informed decisions about pricing, cost management, and overall business strategy.
Cost of Goods Sold and Inventory
While COGS represents the direct costs associated with producing or procuring goods that have been sold, inventory refers to the unsold goods held by a business at a point in time.
The relationship between COGS and inventory lies in their income statement and balance sheet roles.
COGS is an expense item on the income statement which directly affects a company’s gross profit calculation. In contrast, inventory is an asset on the balance sheet representing the value of goods available for sale.
Calculating COGS involves adjustments for changes in inventory levels during a specific accounting period. Businesses must account for the beginning inventory, inventory purchases, and ending inventory to calculate COGS.
An increase in inventory during a specified period generally leads to a lower COGS, while a decrease in inventory typically results in a higher COGS.
Analyzing COGS Using a Cost Sheet
A cost sheet is a comprehensive document that helps businesses track and analyze the costs associated with producing or purchasing goods for sale. Incorporating COGS into a cost sheet is valuable for companies seeking to improve their financial performance and make well-informed decisions.
By analyzing direct and indirect costs and profit margins, a cost sheet can provide a comprehensive understanding of a company’s cost structure and profitability.
A cost sheet can be used to analyze COGS in several ways:
- Cost allocation: By breaking COGS into its various components, a cost sheet can help businesses allocate costs more accurately and identify areas for potential cost savings.
- Cost trends: Tracking COGS over time using a cost sheet can reveal production costs, inventory levels, and profitability trends. This information is useful for decisions about price discovery, inventory management, and cost optimization strategies.
- Benchmarking: Comparing COGS against industry standards or competitors can help businesses identify areas of competitive advantage or disadvantage and make strategic adjustments as needed.
Conclusion
COGS is an important metric that directly affects a business’s profitability and financial statements. Accurately calculating COGS can help companies to make informed decisions, improve their financial health, and avoid unnecessary expenses.
By mastering the concept of COGS and its various components and calculation methods, businesses can make informed decisions and improve their financial health.